What's a "Modular Roundabout"? And Why are More DOTs Installing Them?
They provide a lower-cost alternative to traditional roundabouts and quicker installation. But do they hold up to traffic?
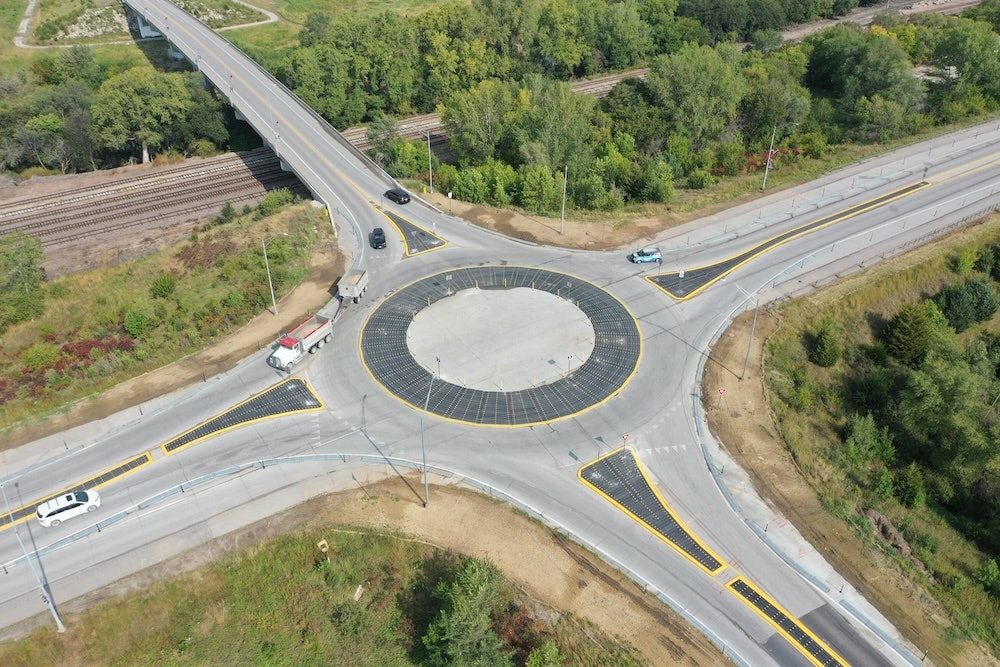
The Nebraska Department of Transportation recently installed a relatively new form of roundabout for converting two-way stops that costs less and can be built faster than a traditional traffic circle.
NDOT's new modular roundabout in Ashland won the "Best Use of Technology and Innovation, Small Project" in the 2024 America's Transportation Awards. The project converted a two-way stop with a roundabout installed in pieces over the existing pavement.
NDOT reported that the modular roundabout cost about 60% less than a concrete traffic circle, and its components are built to last for years.
The Modular Appeal
The Ashland modular roundabout was manufactured under the Vortex brand by ZKxKZ, an engineering firm out of Lexington, Massachusetts, specializing in research and development for military and industrial applications.
The company was founded in 2014 and has so far installed 15 roundabouts in Virginia, Maryland, Florida, Nebraska and California, with three more to be installed this year.
Adam Lanik, vice president of ZKxKZ, sees two forces driving Vortex. One is the increasing adoption of roundabouts in the U.S. The other is the roundabout's high cost and lengthy construction process.
“It’s been ramping up fast ever since about 2000,” he says of roundabout contruction. “Once that happened, people quickly realized, ‘Hey, this is a great tool, but we’re running into some problems. It takes too long to install these things, and they cost way too much.’
“Our primary objective is basically to reduce cost and reduce the time to install. That's what we continue to do to this day, leveraging this quick-build approach. It may sound like a temporary solution, and it can be used in that fashion, but this is designed for a permanent solution.”
All Vortex modular roundabouts, like this "peanut" setup in Virginia, are custom-made to their specific intersection.JMT Engineering
Lanik notes that, among the modular roundabouts it has installed that were billed as “temporary,” only one has been removed. The temporary angle helped some municipalities sell the roundabouts to drivers, who may be resistant at first to a traffic circle but more open to a “temporary” one.
As adoption of roundabouts in the U.S. continues, Lanik sees potential for technology like Vortex’s to help speed up that process. He doesn’t believe modular roundabouts will fully replace traditional roundabout construction, but he expects them to grow, particularly because of the increased driver safety.
“We anticipate, as people become more comfortable and more aware of our technology, they will be able to use that as an effective tool for rapid solutions, taking the same budget they may have and expanding the amount of roundabouts they can do with that same budget and complementing traditional methods,” he says. “I don't fully suspect we'll supplant that, but we'll definitely facilitate in aiding this rapid deployment of roundabouts in the name of increasing safety.”
The Product
The pricetag on a Vortex modular roundabout varies by project, with some as low as $25,000 and others reaching $500,000.
“It's not really the price of our product – it’s how much did they save?” Lanik says. “Nebraska just won an award for a project they did using our product. That one was in the $500,000 range, and the total project cost is about $1 million. But a normal roundabout for that size and intersection would have cost them $4-5 million, so they had significant savings. And it only took three weeks to do the whole project.”
Each Vortex roundabout is designed to last roughly 10-15 years, while the boards will last around 50 years, barring unexpected incidents like crashes.
“Everything is made to last a long time,” says Lanik. “The anchors are all made from stainless steel. So those we'd expect to last 25 years. But we say something slightly lower than that, just to be conservative. And so far, we’ve survived seven years in a very harsh environment up in Canada, so we expect that our estimates are probably pretty accurate.”
One instance where customers do have concerns occasionally, he says, is when they deal with heavy snowplow traffic. If the municipality knows it will be running a large number of plows through the roundabout, Vortex may encourage them to go with a traditional one.
Vortex modular roundabouts can bear weight as high as 80,000 pounds and are made up of stainless-steel hardware with UV-protected polymers.
Each modular roundabout deals with three types of installable pieces: a center island, islands that divide the traffic lanes and “right hand” or diverter islands
From Proposal to Proof
ZKxKZ’s entry into roadbuilding in 2017 came about through the U.S. government-sponsored Small Business Innovation Research program. After the company’s proposal won, it went through two development phases that involved installing two modular roundabouts, in Annandale, Virginia, and in Jackson, Georgia.
“During phase two, before we even installed the trial roundabouts, we actually had our first commercial sale,” says Lanik. “And that was somewhat unproven, at the time, technology. That was up in Canada for three roundabouts.”
ZKxKZ has five employees dedicated to its modular roundabout business and subcontractors to assist with different tasks like material procurement. The modular roundabouts are made in Minnesota.
Lanik says Vortex doesn’t have a direct competitor at the moment, though companies like Zicla, out of Spain, offer products in the same vein, such as installable lane dividers.
Part of the reason Vortex currently stands alone, according to Lanik, is the inability to have a one-size-fits-all modular solution. Still, it’s a possibility Vortex is investigating.
“Entry speeds are different, angles of entry, how many lanes you have, the curvature of the road leading up to it – there's lots of different factors that drive how you design a roundabout, and so you need it to be specific to the intersection,” he says.
Partnering with Customers
Once an order has been placed, Vortex works directly with the customer on the design process. Lanik refers to the company as a partner in the process.
“Because the idea here is to keep costs low, and since we have the experience, we like to help guide the customer through that, to make sure they're saving the most money,” he says.
He clarifies, however, that ZKxKZ staff don’t do the entire design since they are not civil engineers. The team members provide insight based on their experience with previous projects.
“The municipality, or whoever's doing it, has a drawing, and they hand it off to us and say, ‘Make the modular kit fit this site’,” Lanik says. “We take about one to two weeks to do our own drawings and our CAD, then we give that back to the city. Because usually, with a fixed width, you can get pretty close to the dimensions, but every once in a while, you'll be slightly off. So, they [the customer] approve all that. Then it comes back to us, and it's about four to eight weeks to produce it, and then it's about three to five days to ship it to their site.”
Lanik says from the time a customer places an order to the time the roundabout is open usually takes six to 10 weeks, though for larger projects like the one in Ashland, Nebraska, it can be longer.
The Contractor Perspective
Installing a Vortex modular roundabout usually goes one of two ways: either Vortex staff flies to the jobsite and teaches DOT maintenance staff the process or the agency that ordered the roundabout hires a contractor. Lanik says a contractor is used about 40% of the time, and in those instances, Vortex is still available to fly out and give direction.
“The most cost-effective way is to utilize a DOT maintenance crew,” says Lanik. “We provide a very detailed drawing package and installation package that shows how everything goes together. And it's very simple. It's only a few steps – layout, drill, bolt down the anchor – and that's about it. It requires basically a hammer, drill and a few other common tools.
“We have phone support, and then we’ll provide the drawings, if they would like. We also provide on-site assistance, where we can be there anywhere from one day to the entirety of the project to guide people, show them best practices and ensure what they're doing is up to snuff.”
Vortex modular roundabouts have been installed in California, like this one in San Francisco.Vortex
Garret Giesler with K2 Construction out of Lincoln, Nebraska, installed the award-winning Ashland modular roundabout. He says the panels were installed in less than a month, a process that he compares to building a pizza. Giesler says he’d be happy to bid on another modular roundabout project.
“The first week of the project, we had Adam fly in and show us how to get started,” says Giesler. “We started with the center island. We got a survey point of the middle, and we just started laying it out. From there we went all the way around, kind of like a pizza. And we got to the end, and he helped us retrofit a couple things to make it work.
“It was a very easy process, kind of monotonous, but that's OK. We just had to drill holes and anchor the modular panels to the existing asphalt surface with an epoxy anchor. So it was actually a pretty effective process.”
Compared to all the concrete roundabouts he’s handled, the modular version was much faster and cost effective, says Giesler. Additionally, they were able to keep traffic open during the panel installation process.
Giesler says he’s all for the growing presence of modular roundabouts, which have a lot of pros when compared to a traditional roundabout.
“I am also a big concrete guy myself, so I could go either way, but I can see how – it’s effective, efficient, cost effective, [gets done] in a timely manner,” says Giesler. “There’s a lot of pros compared to a concrete roundabout. I think state agencies, counties – if they're looking at doing a roundabout, I wouldn't hesitate to point them toward the modular just because of those benefits.”
The only concern Giesler mentions was over snowplows using the modular roundabout in the winter, but he says there have been hardly any issues.
“I would say, if you're a contractor, don't be afraid to bid one of these,” Giesler says. “We had a concrete crew do the work, and even though it was new to them, the layout and everything was similar. I think you'd be surprised with how profitable it is and how efficient it can be, and how fast you can get the job done.”