Top 5 Causes of Construction-Project Delays Revealed
Waiting on other contractors accounted for more than half of all hold-ups, according to a Touchplan report. See what else made...
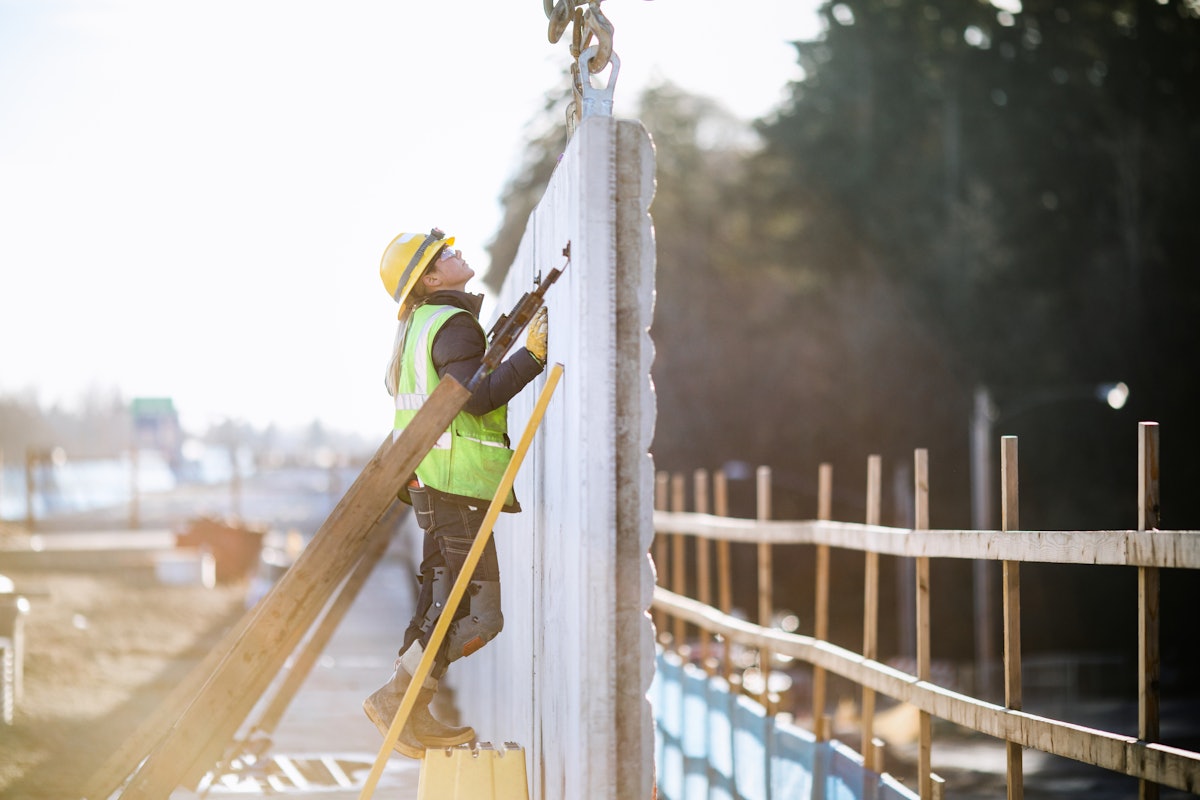
Handoffs between the various trades working on a jobsite are the leading cause of construction project delays, according to a new report from Touchplan, a production planning platform.
The company analyzed data from over 321,042 scheduled construction tasks over the last 12 months to identify the biggest issues behind project delays and budget overruns. Each time a deadline was missed, users reported why their individual tasks were not completed on the promised dates.
Other top issues cited by users included staffing shortages, material or equipment-related issues, design changes and weather, according to the report.
Jason Lyon, vice president of Touchplan Customer Success, provides details about each of the top categories.
1. Handoffs Between Disciplines
Poorly executed handoffs between disciplines are the leading cause of delays, with over 168,000 reported issues.
“One of the cited variances that went into handoff variances was ‘predecessor not ready,’ which is a good example of waiting on the trade ahead to finish their work. This screams handoff. It’s the transition point where one trade partner completes their work and another begins. When these transitions aren’t managed well, it leads to delays,” says Lyon. “Missed handoffs equal replanning, and replanning creates more time spent in planning meetings. You have to work through the challenges that are created as a result of missed handoffs.”
2. Staffing/Crew/Manpower
Staffing issues, including Insufficient staffing or improperly planned manpower, were the second most prominent issue, resulting in 65,000 scheduling variances.
“The construction industry is grappling with a persistent shortage of skilled labor that is driving up costs and delaying projects,” says Lyon. “With rising labor demands and no immediate workforce solutions, contractors must proactively ensure tasks are performed efficiently and disruptions are minimized through proactive, collaborative planning practices.”
3. Material/Equipment
Material or equipment delays caused 44,000 variances during the period.
“Material and equipment-related issues often stem from delays in the delivery of supplies or machinery,” says Lyon. “When materials or equipment aren’t available as planned, it causes significant disruptions and delays in the project schedule.”
4. Design Issues/Changes
The fourth-ranking issue, design Issues or changes, led to 18,000 variances.
“Design issues or changes often result in rework and delays. When there are discrepancies or modifications in the design, it leads to confusion and requires additional time to address these changes, impacting overall productivity,” says Lyon.
5. Weather
Although no team can control Mother Nature, adverse weather conditions caused 17,350 scheduling variances for users.
“The construction industry is extremely vulnerable to delays due to weather events,” says Lyon. “Heavy rain, high winds, and extremely high or low temperatures can put work on hold.”