Modern Construction Methods – Efficient And Sustainable
In the simplest of terms, Modern Construction Methods- MCM are all about the usage of innovative materials, equipment, and techniques so as to build structures. The idea is to lessen the time taken for project execution and the cost of materials and, at the same time, make the building process a lot safer with a […] The post Modern Construction Methods – Efficient And Sustainable appeared first on World Construction Today.
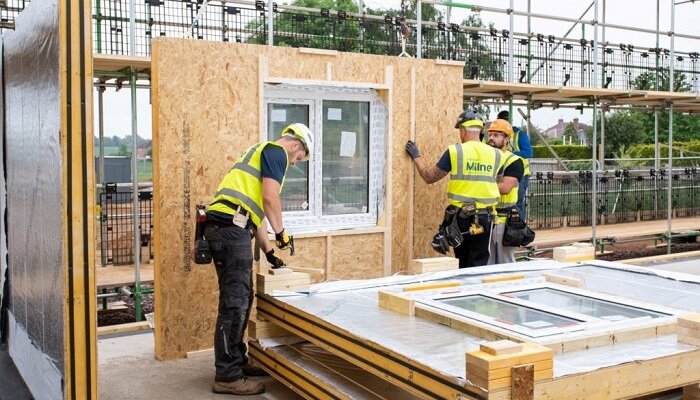
In the simplest of terms, Modern Construction Methods- MCM are all about the usage of innovative materials, equipment, and techniques so as to build structures.
The idea is to lessen the time taken for project execution and the cost of materials and, at the same time, make the building process a lot safer with a prominent amount of what would traditionally be construction work taking place offsite but in a controlled factory setting.
Besides lowering cost by way of reduced time as well as waste, and with a much smaller workforce involved, MCM happens to be a lot more sustainable vis-à-vis other methods of construction that happen to be conventional. It often makes use of fewer CO2 materials and elevates efficiency by using advanced technology. That said, it is a bit strange to see that this practise is taking such a long time to become a part of mainstream operations within the European contractors. If we look back to the 1830s, the first significant evidence of MCM principles was witnessed in the form of the production of a modular house.
So is this once again a scenario of continuing to go ahead with the same things the way they have always been, or are there any other elements that are acting as a barrier to the advancement of MCM? Education, perhaps!
During one of the workshops that was conducted last year on this subject, Akerlof, a consulting firm specialising in MCM services, opined that it is not exclusively about off-site solutions, but it happens to have a much more prominent significance within construction itself.
The practise of putting forth industrial processes within the construction gamut happens to have its sceptics, who in a way are right to say that construction projects very rarely take off in a linear fashion. As a matter of fact, some job sites are described as controlled chaos by the project managers. With regards to this, modular construction would indeed go on to offer benefits that are indeed obvious when it comes to construction time reduction and also making ground zero manageable and much safer. So how is it made possible?
As per the Modular Building Institute (MBI), which happens to be Europe’s leading association in terms of the modular construction segment, the time savings often come at the latter stages of the project, with almost 80% of the on-site building activity gotten rid of. Undoubtedly, this happens to be more advantageous for the construction of educational and healthcare sector buildings, where it becomes almost impossible to shut down as the construction work starts taking place. At present, even in nations where MCM has been embraced, the scale of projects is relatively small. In the UK, for instance, the preparation work is right now going on for a €32 million healthcare centre in Newport, Wales.
The project contractor, Kier Construction, called on Premier Modular in order to manufacture 14 modular units, which went on to total around 513 m2 of temporary space so as to minimise disruption just as the new centre gets delivered. It is well to be noted that the modern facility is anticipated to be operational by January 2025.
As per Premier Modular, it took only 4 weeks for the facilities to get delivered and also installed at a cost of €858,000.
The temporary units measured 12 x 3 m each, with a ceiling height of 2.7m. As per Premier Modular, the flexible system goes on to allow changes in the facility during the course of construction. This includes catering to the need for more units as well. The UK government has gone on to embrace the MCM principles, thereby offering millions of pounds so as to speed up their adoption. Algeco, which happens to be a modular solution firm, recently incurred a great deal of benefit through this drive. It went on to win contracts amounting to almost €38 million pertaining to supplying secure prison units for the Ministry of Justice.
In the scenario of a growing shortage when it comes to secure accommodation for prisoners, the UK government has already initiated a plan of €4.5 billion that will go on to deliver another 20,000 places. Overall, Algeco is expected to deliver more than 500 units in 2023, which includes securing sleeping accommodations for almost 1,000 prisoners. The company has gone on to develop a Rapid Deployment Cells Project by way of creating a new design that can be rapidly deployed across a variety of sites so as to help meet short-term demands when it comes to the prison system.
Although the quick deployment and flexibility of such a scale of units are impressive, they can also lead people to suspect that modular construction is only viable for single-story buildings. As a matter of fact, the UK also happens to host the world’s tallest modular structure, which is 135 m in height—the Ten Degrees twin towers.
These 38- and 44-story towers aren’t only tall when it comes to modular building scale, but they are as simple as they are tall. Each of the building’s apartments was manufactured off-site by Tide Construction as well as Vision Modular Systems. The individual structures were then just stacked so as to create the towers.
Designer HTA goes on to state that the construction of this structure required 67% less energy as compared to the traditional means of construction. The Modular Building Institute did maintain the fact that modular buildings happen to be stronger in nature than the ones that are built onsite, as each of the modules happens to be engineered to single-handedly withstand the transportation and craned to the foundations. Besides, the manufacturing plants that happen to be developing the modules adhere to strict protocols pertaining to quality and make sure that each element of the building gets fabricated to the highest standards of construction.
The fact is that for a modular project to effectively fulfil its promises pertaining to efficiency as well as sustainability, they have to be built into the project from the very beginning.
It is well to be noted that everyone from the team that is taking care of initial design to fabricators and the teams working at the site should very well understand the MCM principles and then only put them into practise. Apparently, Building Information Modelling happens to be a core software piece for the construction business that examines modular processes.
BIM, undoubtedly, is a critical tool from the outset that helps in aiding the design elements. It also helps the workflows pertaining to design and fabrication, gives a 3-D visualisation of the project, and assures an exact, desired execution as far as the construction phase is concerned. Apart from this, material choice also happens to be a key element of MCM projects, with BIM making sure that only the right materials get selected, both in terms of the integrity of the structure and the reduced cost of execution.
The post Modern Construction Methods – Efficient And Sustainable appeared first on World Construction Today.