The Overlooked Wheeled Excavator – They Do More Than You Might Expect
If you think they’re just excavators with no tracks, you’re missing the point.
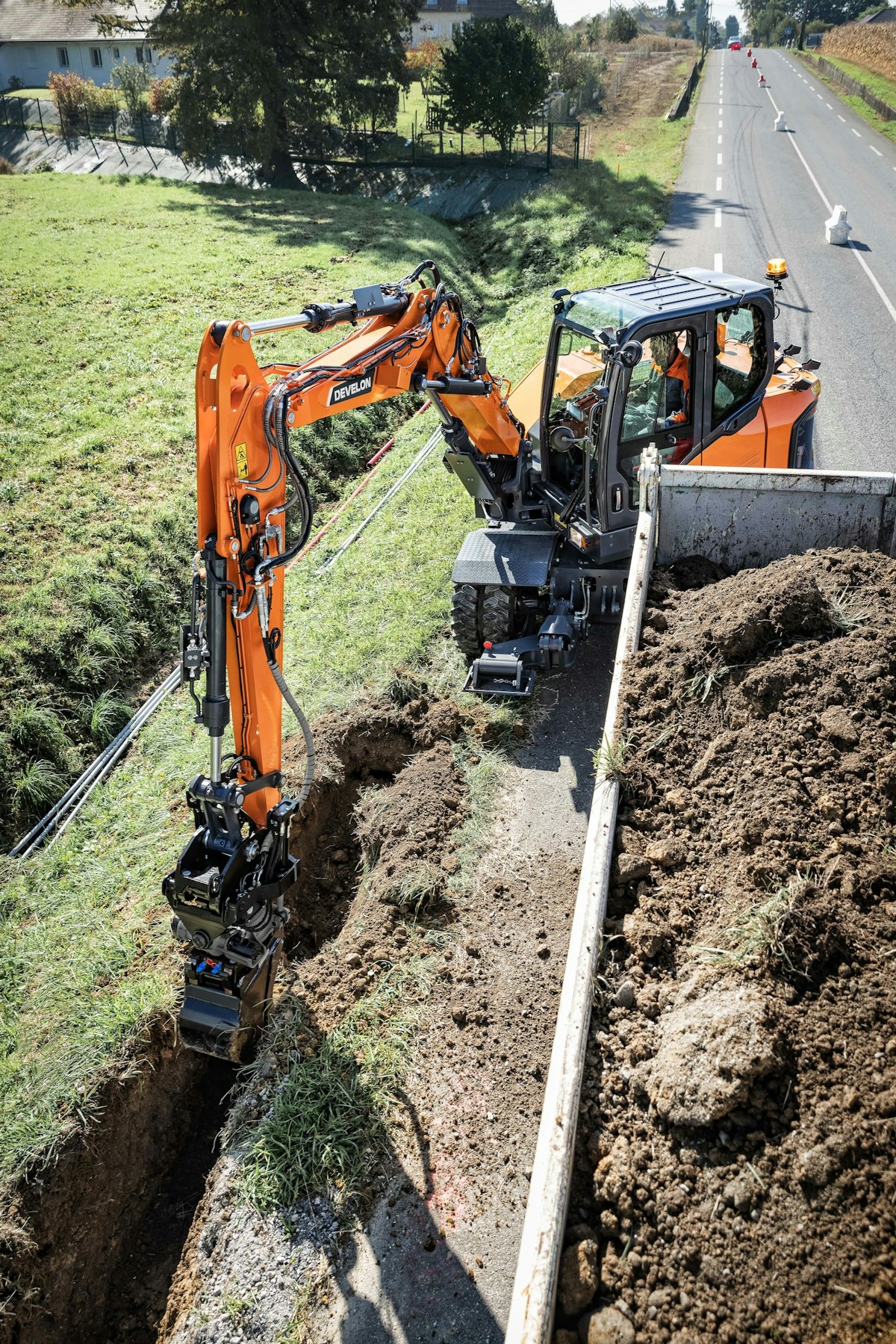
The initial mental image for many U.S. contractors of wheeled excavators is a machine that’s going to get stuck in the mud, tip over during a heavy lift or just be a wimpy alternative to a tracked excavator.
But an increasing number of contractors are seeing the wheeled excavator as its own entity – an extremely versatile machine designed to do things and go places crawler models and other types of equipment can’t, or won’t be as efficient.
Manufacturers are appealing to the gradually growing market with new models introduced here in the past year.
Takeuchi debuted its first wheeled excavator for the U.S. in 2023. Case recently re-entered the U.S. wheeled excavator market with a new model. Develon has rolled out its first mini wheeled excavator, and Wacker Neuson redesigned its largest wheeled excavator.
Caterpillar announced last year it has produced 50,000 wheeled excavators since it began offering them in 1984.
“Offering quick movement on the jobsite and from site to site without damaging the ground, the wheel excavator proved to be a game changer for contractors working in congested areas and markets with mature infrastructure,” said Brian Abbott, vice president of product management for Cat’s excavation division, when marking the company’s milestone.
To be sure, the wheeled excavator is not for everyone, but it could fit into your fleet better than you might expect.
A Toolcarrier in Disguise
Wacker Neuson redesigned its largest wheeled excavator, the EW100, to add more horsepower and hydraulic flow for running a variety of attachments.Wacker Neuson
But when paired with a tiltrotator – another popular device in Europe gradually making inroads in the U.S. – the wheeled excavator becomes transformed into a versatile toolcarrier. With a tiltrotator, the same wheeled excavator can also run forks for loading and unloading trucks. You can also spin a bucket around and use it as a loader, not to mention the added maneuverability a tiltrotator offers for traditional digging and grading operations.
Typically, wheeled models offer a different hydraulic system than tracked excavators for handling various attachments.
“The advanced hydraulic design, plumbed differently than conventional excavators, allows them to go beyond digging to operate a range of hydraulic work tools to increase application flexibility,” according to Abbott.
For example, Volvo crawler excavators use a hydraulic system that delivers full pressure at once wherever it needs to go, including swing and drive motors. Its wheeled excavators use load-sensing hydraulics that focus on sending hydraulic oil where it needs to go for the attachment, such as the boom or arm, and not where it isn’t needed. Though more expensive, the system is better for running attachments, such as mulching heads and augers.
Many newer models come ready for tiltrotators, including Wacker Neuson’s 10-ton EW100, which was released last year.
“You’ll be able to take a tiltrotator from Rototilt, Steelwrist or Engcon, plug it into the machine, go right to your display, select the brand, and it will adjust the controls out of the box,” said Jay Quatro, commercial product manager at Wacker Neuson. “There are no more additional packages needed and no more additional control systems. It all comes from the factory that way.”
Going Where Others Can’t
Case re-entered the North American wheeled excavator market last year, starting with its short-radius WX175E SR.Case CE
Because they are more compact, they only take up one lane of traffic. That makes then handy on road projects, including right-of-way management and roadside utility work.
Some of the models have four-wheel-steer and crab steer, as well as tight tailswing, for maneuvering into confined spots, such as narrow alleys, between buildings and on sidewalks.
When it comes to stability, many models come with outriggers to brace the machine while digging. The dozer blade can also be used to increase stability.
“A lot of folks feel like wheeled excavators may not be as stable as tracked excavators, and that's simply not true,” said David Caldwell, Takeuchi national product manager. “When you lower the rear stabilizers and the blade, you have a very stable working platform.”
Hit the Road
Mecalac's MWR9Mecalac
That was one reason Luke Parmenter, owner of L&S Earthworx in Ellensburg, Washington, switched from a 5-ton crawler excavator to Mecalac’s 9-metric-ton wheeled 9MWR.
“I wanted wheels because I do a lot of work on hard surfacing, and I'm just tired of wearing tracks out and spending a long time moving around jobsites,” he said.
A Backhoe Alternative?
Some even view it as more of an alternative to a backhoe than a tracked excavator because of its compactness, road speed and increased productivity.
Volvo claims its EW60E wheeled excavator outperforms a similar-sized backhoe in trenching and pool digging, cutting work time in half and using four times less fuel.
“While the excavator in any form will never completely take over backhoe loaders, the wheeled excavator is a good cost-efficient alternative if you require high mobility,” Volvo says.
Check out Volvo’s video “Backhoes vs. Wheeled Excavators” below:
Growing Market
Takeuchi, in launching its first wheeled excavator to the U.S. market last June, cited urban growth as one reason jobsites will start to see more wheeled excavators.
“As cities grow and population centers grow, you'll start to see more because you need more versatility to move through those jobsites quickly and efficiently,” Caldwell said.
Case offered similar sentiments when re-entering the wheeled excavator market in 2023 with its WX175E SR, adding that the cost of ownership of wheeled excavators is lower than crawler models, as those tracks need maintenance and wear out.
“Jobsites are becoming tighter,” said Diego Butzke, Case product manager. “Transporting steel-tracked equipment relatively short distances can be challenging, and steel tracks represent a large portion of the lifetime owning-and-operating costs of any piece of heavy equipment.”
Takeuchi's TB395W features a double-boom design, which provides more reach and an ability to dig and lift closer to the machine.Takeuchi