Common Issues with Construction Tools and How to Fix Them
Have you ever been in the throes of a significant construction project, only to find your tools refusing to cooperate when you need them the most? It’s a situation that can derail any project. By understanding construction tool maintenance, you can turn these tools from potential liabilities into reliable teammates, bringing your project’s vision into […] The post Common Issues with Construction Tools and How to Fix Them appeared first on World Construction Today.
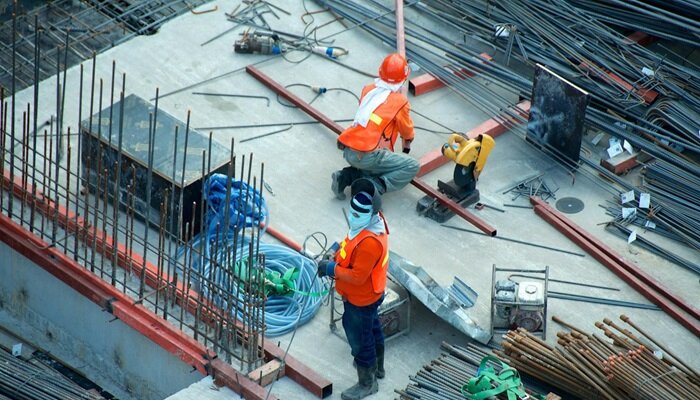
Have you ever been in the throes of a significant construction project, only to find your tools refusing to cooperate when you need them the most? It’s a situation that can derail any project. By understanding construction tool maintenance, you can turn these tools from potential liabilities into reliable teammates, bringing your project’s vision into sharp, triumphant focus.
Common Electrical Problems in Construction Tools
Tools are the backbone of every successful project. Unfortunately, they are often subject to wear and tear, leading to various operational challenges. Recognizing these potential issues early and taking proactive steps can make all the difference in keeping your equipment running smoothly.
By addressing these challenges head-on, you can ensure your tools remain reliable partners in every project, no matter the demands.
Power Supply Issues
A robust power supply is the cornerstone of any efficient construction tool, yet it is often a source of frustrating interruptions. Tools may falter during operation if power delivery is inconsistent or inadequate.
One common issue is fluctuating power, known as “power dips.” This can be a result of a damaged cord, requiring immediate repair to prevent tool wear and maintain performance integrity.
Troubleshooting power issues involves checking the health of the power grid and tool connections. By assessing and replacing worn cords, fuses, or circuit breakers, you’ll ensure continuous and reliable power.
Motor Failures
Motor failures in construction tools are often attributed to lack of regular maintenance, impacting efficiency and productivity on the job site.
In 2022, industry statistics revealed a significant number of motor-related issues stemming from dust accumulation and overheating. Such conditions can lead to motor burnout, necessitating costly repairs or replacements.
Fortunately, it’s remarkable how regular cleaning and inspection can extend a tool’s lifespan. Dust removal, coupled with appropriate lubrication, ensures motors run smoothly and reduces the risk of premature failure.
Overheating Problems
Overheating issues can disrupt tool performance, leading to shorter lifespans and increased repair costs without timely intervention. To address this, optimal ventilation within a tool’s casing is paramount.
Accumulated debris can stifle airflow, intensifying heat retention, which exacerbates overheating. Cleaning out vents and ensuring unobstructed airflow is crucial to mitigate this. Additionally, maintaining proper lubrication can reduce friction-induced heat, which significantly contributes to overheating.
In some cases, advanced methods like induction heat treating can further enhance the durability of key components by making them more resistant to high temperatures and wear, adding an extra layer of protection against overheating.
Recognizing warning signs is a crucial aspect of construction tool maintenance. If tools start to emit unusual odors, experience a sudden decrease in power, or become excessively hot to touch, immediate attention is required.
Mechanical Breakdowns and Their Fixes
Construction equipment is often subjected to intense demands, which can lead to various mechanical and operational challenges over time. However, with the right maintenance practices, many of these issues can be mitigated or entirely avoided, ensuring tools perform at their best.
Addressing problems proactively and implementing preventive measures not only reduces the risk of downtime but also extends the lifespan of essential equipment.
Gear Malfunctions
Firstly, gear malfunctions often arise from a misalignment or excessive wear, which could stem from frequent use or improper maintenance practices.
Regularly scheduled inspections, adjusting positions, and replacing worn-out gears are fundamental steps in maintaining gear integrity. Identifying symptoms such as unusual grinding sounds or difficulty in gear shifting is also crucial.
Broken Seals and Gaskets
Seals and gaskets are vital components ensuring the smooth operation of construction tools. When seals and gaskets become compromised, equipment may begin to show signs of leaking, which can lead to decreased performance.
To effectively manage such issues, it’s essential to adhere to regular inspection schedules. Checking for early signs of wear or damage can indicate when it’s time for replacement. Using the best mechanical seals in your equipment can further enhance durability, reducing the risk of leaks and ensuring long-term reliability.
Embracing preventive maintenance allows you to address small issues before they become major challenges, safeguarding productivity and fostering the longevity of your tools.
Lubrication and Friction
Few factors are as crucial as addressing the challenges of lubrication and friction. The right choice of lubricant can dramatically extend the operational lifespan of various construction equipment, leading to an increase in efficiency and a reduction in costly downtime.
This extends to choosing the appropriate grease or oil. Make sure surfaces are clean and dry before lubrication is applied. This seemingly small action can create the difference between smooth sailing and frustrating malfunctions mid-project.
Issues with Pneumatic Tools
Tools, particularly pneumatic ones, are highly susceptible to issues that can disrupt their functionality, affecting both productivity and project success. Addressing these issues before they become serious problems can save valuable time and resources on the job site.
A proactive approach to tool maintenance, focusing on key problem areas, can prevent unexpected downtime and ensure that your equipment operates smoothly under even the most demanding conditions.
Leaking Air Hoses
When faced with leaky air hoses, a thorough inspection is a paramount first step. Begin by examining the connections, as loose fittings often result in air leakages. Ensure the clamps are tightly secured and replace any worn-out or damaged couplings as needed.
Checking for wear and damage in the hose itself is crucial. If any cracks or holes are detected, replacing the hose is the optimal solution to avoid further air loss and maintain efficient operation.
Pressure Inconsistencies
Pressure inconsistencies in pneumatic tools can lead to a range of issues, from uneven performance to complete operational failure.
To ensure smooth tool operation, follow these steps:
- Evaluate Compressor Performance: Check if the air compressor is reaching the required PSI, and adjust it according to the tool’s manual if necessary.
- Examine Regulator Settings: Make sure the regulator settings match the optimal pressure output for the tool to avoid unstable performance.
- Use a Quality Pressure Gauge: Regularly use a reliable pressure gauge to monitor pressure levels and identify issues early.
- Maintain Consistent Inspections: Conduct regular maintenance and inspections of the compressor, hoses, and regulator to prevent unexpected downtime.
General Wear and Tear Over Time
This gradual decline, though often overlooked in a bustling construction environment, affects the tool’s efficiency, reducing its productivity. Components such as blades, drills, and motor brushes are commonly susceptible to such degradation.
Proactively, it’s beneficial to establish a thorough maintenance schedule for all tools. In doing so, timely replacements of worn elements ensure that performance levels remain high, minimize safety risks, and enhance overall project outcomes.
Indeed, by committing to proactive maintenance and replacing compromised components at appropriate intervals, you empower your team for success. Such strategic oversight fosters an environment where your construction tools can continuously function with precision and reliability, driving optimal results with every application.
Preventative Maintenance for Long-Term Durability
Preventative maintenance is essential for ensuring long-term durability and efficiency in your tools.
Follow these steps to maintain peak performance and extend tool life:
- Routine Inspections: Regularly inspect your tools to identify potential vulnerabilities and address them early to prevent costly repairs and downtime.
- Cleaning and Lubrication: Consistently clean and lubricate tools to reduce wear and minimize friction, significantly extending their lifespan.
- Commitment to Excellence: View preventative maintenance as an ongoing commitment that enhances tool performance and reliability, supporting long-term success.
- Understand Each Tool’s Needs: Take the time to understand the specific maintenance requirements of each tool, enabling informed decisions that benefit your projects.
- Proactive Care: Prioritize proactive, rather than reactive, maintenance to turn potential obstacles into opportunities for better results.
Conclusion
In construction, the reliability of your tools is key to delivering successful projects on time and within budget. By understanding the common issues that can arise and taking a proactive approach to maintenance, you can ensure your equipment remains efficient and durable.
Addressing problems early, implementing regular inspections, and prioritizing preventive care will not only extend the lifespan of your tools but also minimize costly downtime. With the right strategies in place, your tools can consistently perform at their best, keeping your operations running smoothly and your projects on track.
The post Common Issues with Construction Tools and How to Fix Them appeared first on World Construction Today.