Unlock the Benefits of Compaction Rollers in Construction Projects
Discover how compaction rollers enhance construction projects with increased stability, durability, and efficiency. Learn the key benefits of using compaction rollers to ensure a strong foundation and improved project outcomes.
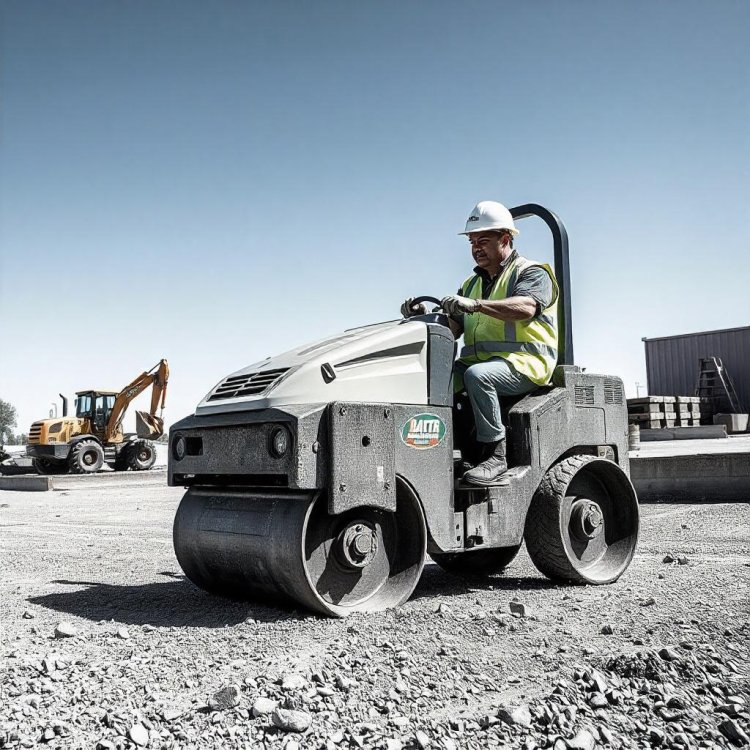
In the world of construction, ensuring a stable and durable foundation is crucial to the success and longevity of any project. This is where compaction rollers come into play. These powerful machines are specifically designed to compress soil, gravel, and other materials, creating a solid base for roads, buildings, and other structures. But the benefits of compaction rollers go far beyond just flattening the ground. They enhance efficiency, improve material durability, and ensure the stability of your construction projects.
Are you operating on a construction task and searching for the most practical way to compact ground? If so, then compaction rollers are your finest bet. These machineries compact soil, asphalt, stone, and other materials for different jobs, including building bases and paving roadways. This blog post will debate how compaction rollers operate and their benefits when used in construction tasks.
Types of Compaction Rollers
Compaction rollers come in different shapes, sizes, and varieties. The most famous kind is the smooth drum roller, created to deliver optimal compaction capability with its heavy operating weight. Pneumatic rollers are another famous choice as they have static linear load and static pressure abilities, making them appropriate for use on different soil subgrades. Padfoot rollers are also perfect for cohesive soils, while single-drum soil compactors are ideal for large areas such as parking lots, driveways, and more.
Benefits of Using Compaction Rollers
The basic advantage of compaction rollers is that they can quickly cover large sites with minimal effort from a single individual. This makes them ideal for any construction task where duration is of the essence. Compaction rollers also deliver consistent compaction, confirming that all compact areas get an exact amount of pressure from the machine’s fixed power. This allows us to stop any weak or irregular spots on the surface that could direct to problems later on down the line. Ultimately, these machines can be utilized for a broad range of applications, including asphalt paving machines (for sealing objectives), making bases (on sensitive areas), or just smoothing out gravel or dirt grounds over big areas (such as parking lots).
Typical Compaction Roller Problems and Answers
Construction needs compaction rollers. It would help to have reliable equipment to compress asphalt, gravel, or other jobs. A compaction roller that can manage different soil subgrades and create even compaction is a must. Typical compaction roller problems and explanations are here.
Compaction Roller Types
Vibrating plates are useful for cohesive grounds like clay and silt. In contrast, single-drum soil compactors are appropriate for extensive areas and are easy to use. Stationary linear load rollers are useful for compacting asphalt and different materials. In contrast, Padfoot rollers are perfect for sealing temperate areas like making foundations. Roadwork and other heavy-duty functions need pneumatic rollers.
Smooth Drum Roller Compacting Smooth drum rollers are famous compaction equipment for their optimum capability and operating weight. The machine’s weight delivers uniform compaction across different soil surfaces without damaging concrete or asphalt pavements. In addition, the machine’s drum vibrates to develop a homogeneous surface for sealing, asphalt pavement, or gravel highways.
Troubleshooting Operators often require assistance keeping drum speed, which may direct to irregular compaction. To avoid this issue, ensure your single drum roller has sufficient capacity to address diverse soils and materials to keep speed throughout the procedure. Creating static linear load for gravel and asphalt pavements is another difficulty. Ensure your roller has an excellent weight to produce enough static force to compress the material throughout processing to create a uniform surface after compaction. Ultimately, check all safety precautions before using equipment to evade fatal injury or death.