Carbon Challenges Facing Cement Demands Considerable Lifting
Cemonite has gone on to create a concrete that happens to be completely free from ordinary Portland cement, the traditional material that happens to be used to bind the concrete together and which is indeed responsible for 90% of the carbon emissions. This also happens to be solving yet another environmental issue by finding a […] The post Carbon Challenges Facing Cement Demands Considerable Lifting appeared first on World Construction Today.
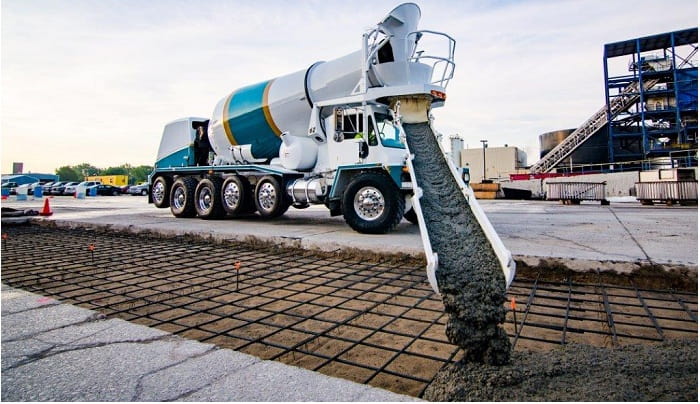
Cemonite has gone on to create a concrete that happens to be completely free from ordinary Portland cement, the traditional material that happens to be used to bind the concrete together and which is indeed responsible for 90% of the carbon emissions. This also happens to be solving yet another environmental issue by finding a way for tailings.
It is well to be noted that Cemonite process happens to avoid the usage of limestone, says Stian Rossi, who happens to be the chief commercial officer of the company. All of this happens to mean that there is no energy-intensive calcination stage in case the cement kilns need to be fired up to temps that are really scorching, and that too for weeks so as to create the clinker that gets ground up in order to make OPC.
The cement, apparently, has been used in a number of pilot projects and has indeed gone through rigorous strength tests, as per Rossi.
Notably, ordinary Portland cement, which happens to be a generic name rather than a mere brand, gets made by heating a mix of limestone as well as clay to 1400C in kilns that are powered by fossil fuels. This goes on to convert limestone into lime, thereby releasing CO2 in the process. The nodules that are leftover are called clinker, and those ground up to form OPC. However, the process means that every tonne of cement happens to be producing around 622kg of CO2.
The fact is that the alternatives to fossil fuels so as to power the kilns like biomass, green hydrogen as well as electricity happen to be still some way off as per concrete materials specialist at Arup, Fragkoulis Kanavaris as they cannot touch the temps that are required.
One more controversial way so as to attain the needed heat is co-processing. Although the research suggests that it can cut greenhouse gas emissions by a tenth, there are alarms raised over there toxic emissions and effect on recycling endeavors.
As a matter of fact, the Heidelberg Materials approach happens to be focused on making use of difficult to recycle waste like plastics, which happen to be dirty, meat and bone meal, tyres as well as certain kinds of solvents, as well as paints that would in a way otherwise would get thrown. Known as alternative fuels and raw materials- ARF, they happen to replace fossil fuels sans affecting the final products’ quality.
In addition to using the energy content of the waste as well as decreasing the CO2 emissions from the kilns, the company happens to embed ashes into clinker in the form of a raw material. It is worth noting that Heidelberg is looking forward to elevating the ARF proportion in its fuel mix to 45% by 2030.
There are companies that happen to be making use of alternative materials known as supplementary cementitious materials- SCMs in order to replace the clinker proportion in the OPC and also form geopolymer cement. These happen to include waste materials like fly ash, which is a byproduct of the coal sector, as well as metal slag, which happens to be left over from steel.
There is a possibility that while their new supplies are going to become scarcer since coal will be phased-out, there is plenty which is still available as legacy from the sector, remarks the Chief Executive, World Cement Association, Ian Riley.
There also happens to be a growing popularity of calcined clay, which is formed due to burning clay, which, by the way, happens to be the most abundant substance on earth, and also using crushed powder as an OPC substitute.
It happens to offer similar strength performance, just like OPC; however, it comes with a third of the carbon footprint. And since clay is especially abundant in the Global South, it could indeed prove to be a significant way when it comes to cutting emissions coming from the infra boom.
It is worth noting that Arup has been investigating probabilities wherein it can make use of 5 million cubic meters of soil as well as clay that’s excavated in building the HS2 high-speed rail link, says Kanavaris, thereby reprocessing it into sustainable concrete and also saving almost 150mn pounds when it comes to landfill costs.
While this research may be late so as to have a dramatic effect on HS2, the work has gone on to reveal a new avenue towards high-value repurposing when it comes to waste clays and can as well be applied across other Arup projects throughout the world.
Apart from replacing clinker, companies happen to be also looking for additives that can be mixed along with the concrete, some aiding to harden the cementitious materials that are supplementary and others to decrease the amount of OPC that is required.
All these happen to include carbon nanomaterials like graphene, and Arup is indeed working with the University of Manchester in Britain, where the material was first characterized in 2004. While taking out the portion of OPC from the mix leads to concrete that’s weaker, one can rebuild the strength by way of adding meager amounts of less carbon-intensive graphene. Interestingly, the trials are at present underway at the concrete railway sleepers.
Waste happens to be yet another area wherein the concrete manufacturers could as well claw back their emissions. It is estimated that 2.6bn tonnes of CO2 emissions could be stricken off by way of applying circular solutions to concrete by 2050. However, the introduction of these solutions is going to need a traditionally conservative industry so as to add adapt as well as embrace fresh ways in terms of working.
Not overly specifying the concrete quality is one core area Riley sees as potential carbon saving. He adds that the concrete that they are making use of in a lot of cases is way better than it needs to be, and it has, as a matter of fact, become the norm to specify one grade of concrete that is the highest for the entire site of construction, yet the higher the grade, the higher the production emission.
One of the major changes that both Rossi and Riley expect are needed for the alternative clinkers so as to catch on is to move away from the recipe formula when it comes to concrete, and this would certainly, in a way, open up the idea and field for certain other materials.
The post Carbon Challenges Facing Cement Demands Considerable Lifting appeared first on World Construction Today.