Advancing Metal-Cutting Technology: Transformative Innovations, Sustainability, and the Future Workforce
1 ) What recent advancements in metal-cutting technology have had the most transformative impact on efficiency and precision? For STUDER, WireDress®, Smartjet® and C.O.R.E. technologies are of central importance, as they contribute significantly to our process`s efficiency, precision and innovative strength. SmartJet® technology efficiently controls cooling and energy consumption, reducing coolant consumption by up to … The post Advancing Metal-Cutting Technology: Transformative Innovations, Sustainability, and the Future Workforce appeared first on Machine Insider.
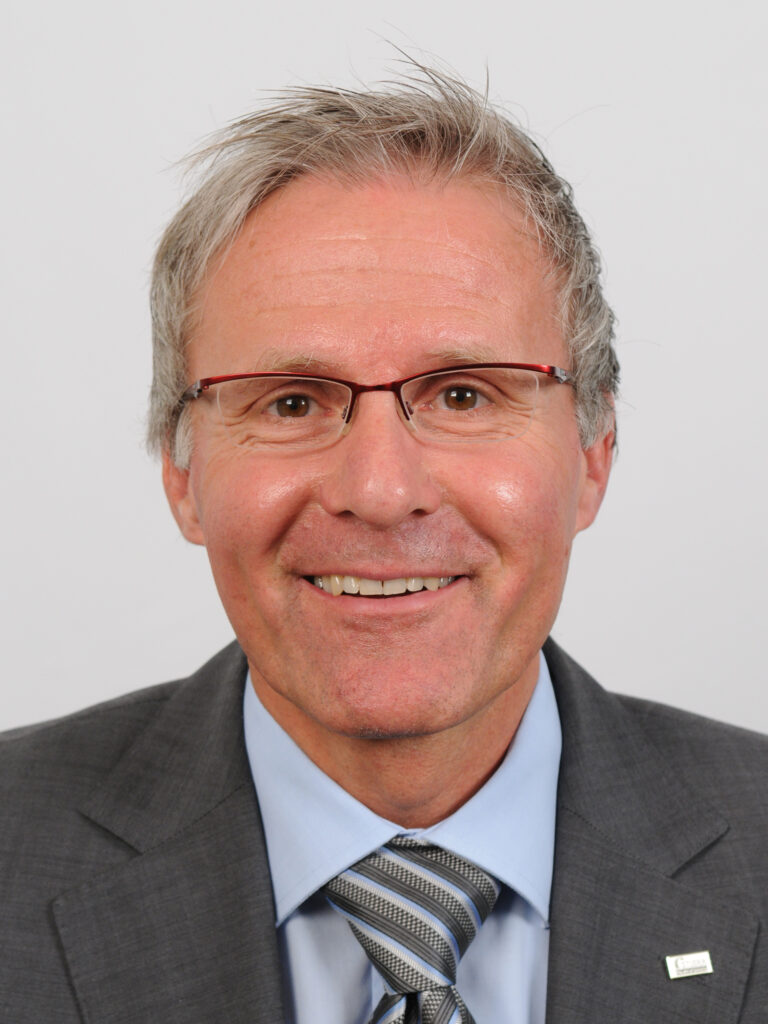
1 ) What recent advancements in metal-cutting technology have had the most transformative impact on efficiency and precision?
For STUDER, WireDress®, Smartjet® and C.O.R.E. technologies are of central importance, as they contribute significantly to our process`s efficiency, precision and innovative strength.
SmartJet® technology efficiently controls cooling and energy consumption, reducing coolant consumption by up to 40% and energy consumption by up to 50%. This resource-saving solution is ideal for companies that want to combine sustainability and cost efficiency.
WireDress® technology enables metal-bonded CBN and diamond grinding wheels to be dressed directly in the machine. This results in up to 30% higher grinding performance and significantly extends the service life of the grinding wheels, minimizing downtime and increasing productivity.
C.O.R.E. technology also simplifies machine operation through digital assistance systems. Functions such as Remote Service enable quick troubleshooting, while the Service and Production Monitor keep an eye on maintenance work and production processes in real-time. These smart solutions increase efficiency and ensure smooth operation.
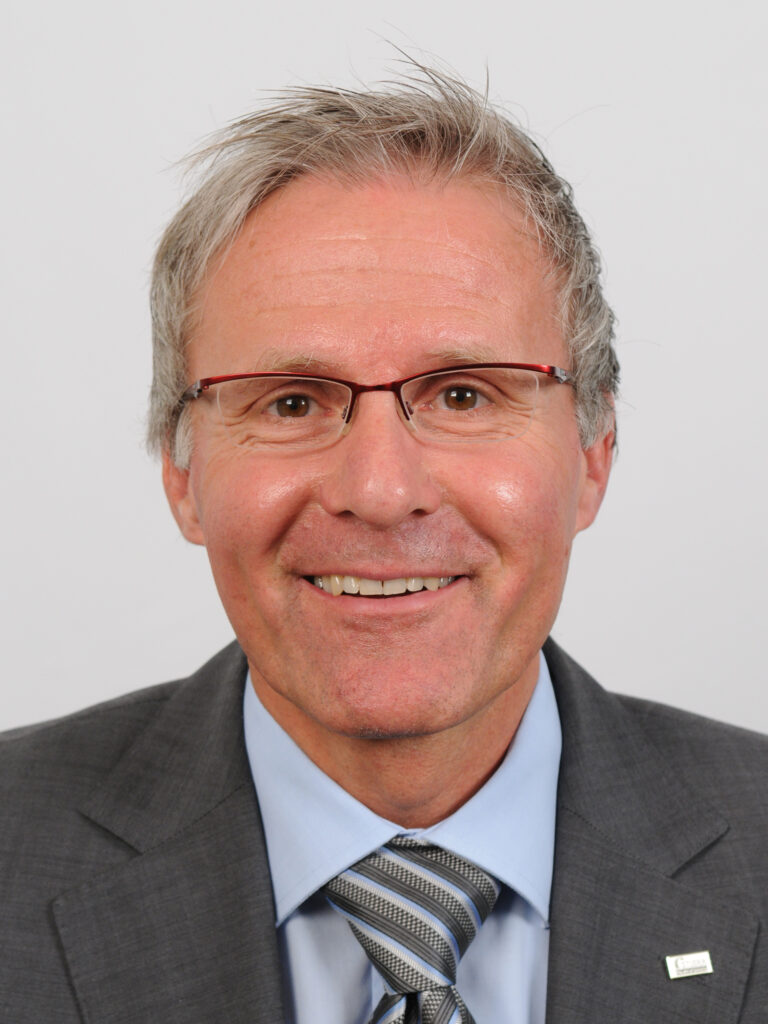
2 ) How is the industry adapting to sustainable manufacturing practices, and what specific initiatives are helping to reduce environmental impact?
STUDER is a BluePlus Alliance Member. The Blue Competence initiative of the German Engineering Federation (Verband Deutscher Maschinen- und Anlagenbau – VDMA) actively promotes sustainability in the engineering industry. The initiative aims to publicize sustainable solutions in the industry that support innovative energy concepts, efficient use of scarce resources and an improvement in the quality of life.
3 ) With digitalization reshaping manufacturing, what new skills are essential for today’s workforce, and how is the industry addressing the skills gap?
Given the increasing digitalization in manufacturing, new qualifications, such as in-depth knowledge of PC and network technology, are becoming increasingly important, as modern manufacturing processes rely on digitally networked systems. Skills in the operation and maintenance of IT systems, and an understanding of data security and digital communication, are crucial to ensuring smooth production.
Despite these developments, traditional grinding know-how remains an essential core skill. This is because the control systems of modern machines, which offer considerable assistance through technological support such as suggestions and simulations, do not replace the experience and expertise of the user. The ability to manually analyze, adjust and optimize processes remains invaluable. Combining digital expertise with traditional manufacturing know-how ensures that the workforce can meet the demands of the modern manufacturing world and actively shape it.
4 ) What trends are driving the current demand for metal-cutting solutions, and how do you foresee the industry adapting to these trends?
The current demand for metal-cutting solutions is driven by several important trends. One of the key drivers is new abrasives that offer higher performance, longer tool life and increased efficiency thanks to advanced materials and improved technology. These innovations enable more precise machining while also reducing costs.
Another important trend is multifunction machines, which combine different processing steps in a single system. These machines help to optimize production processes, save space and time, and increase flexibility in manufacturing.
In addition, complete machining is becoming increasingly important. Customers expect solutions that enable workpieces to be completed in a single operation, to minimize rework and eliminate sources of error.
The industry is adapting to these trends by increasingly focusing on innovative technologies, developing flexible machine concepts, and adjusting its processes to the increasing demands for precision and efficiency.
5) What do you view as the most significant challenges facing the metal-cutting industry today, and what steps is your organization taking to stay competitive?
For us, the availability of qualified personnel is one of the biggest challenges. To meet this need, we have developed a highly specialized training and development program tailored to the needs of our industry. We currently offer apprenticeships in eight different occupations, with apprentices accounting for around 10% of our employees. By continuously investing in training, we not only ensure that we have a new generation of skilled employees, and promote the sustainable development of the industry as a whole.
Do visit – https://www.studer.com/de/
The post Advancing Metal-Cutting Technology: Transformative Innovations, Sustainability, and the Future Workforce appeared first on Machine Insider.