8 Reasons to Automate Your Asset Tracking Tasks Today
Construction businesses make significant financial investments in the tools, equipment, and machinery you need to complete projects correctly and efficiently. As the saying goes, "you gotta have the right tool for the job." Unfortunately keeping track of those assets across multiple jobsites and warehouses is a challenge, and all too often expensive items can “walk away” costing contractors significantly. Beyond replacement costs, the real toll on constructions businesses includes lost productivity, increased labor costs, and disruptions to project timelines. To combat this, contractors must track their high-value, mission critical tools and equipment. But the process can be incredibly tedious, time consuming, and full of human error. After all manually counting items in your warehouse or on your jobsite and trying to document every transfer accurately is a ton of administrative overhead that takes your employees off tasks that push projects forward. Asset management has always been a challenge. But in today’s landscape—marked by the labor shortage, high equipment and materials costs, and supply chain uncertainty—managing and tracking your assets manually has grown increasingly difficult. That’s why contractors have turned to automation. Automation can eliminate repetitive asset tracking tasks provide each departments with the data they need, improving operational efficiency and unlocking better project outcomes. In this article, we’ll break down 8 ways asset tracking automation helps your field, warehouse, and back-office teams increase productivity to accelerate project delivery and increase profit margins.
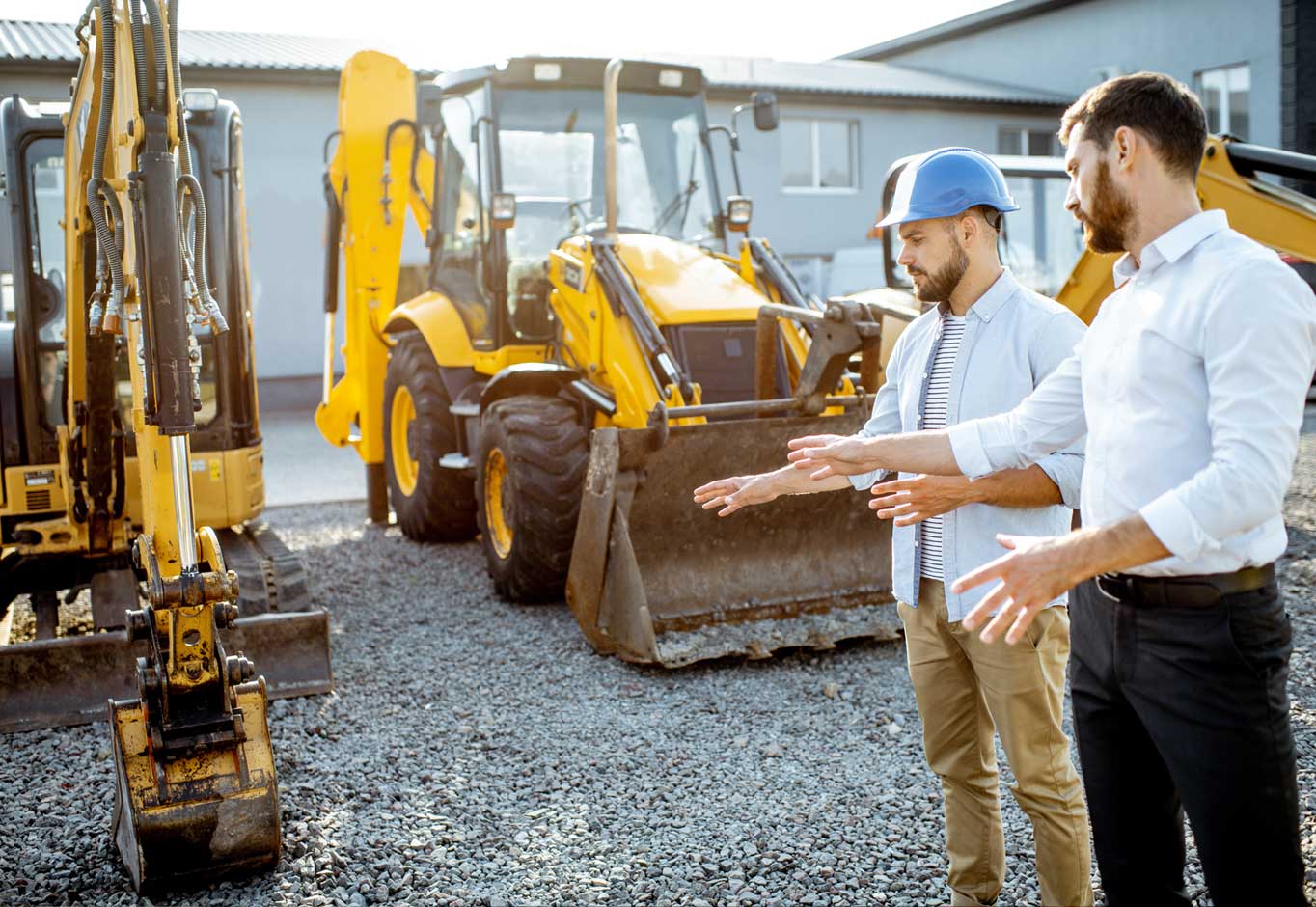
Construction businesses make significant financial investments in the tools, equipment, and machinery you need to complete projects correctly and efficiently. As the saying goes, "you gotta have the right tool for the job."
Unfortunately keeping track of those assets across multiple jobsites and warehouses is a challenge, and all too often expensive items can “walk away” costing contractors significantly. Beyond replacement costs, the real toll on constructions businesses includes lost productivity, increased labor costs, and disruptions to project timelines.
To combat this, contractors must track their high-value, mission critical tools and equipment. But the process can be incredibly tedious, time consuming, and full of human error. After all manually counting items in your warehouse or on your jobsite and trying to document every transfer accurately is a ton of administrative overhead that takes your employees off tasks that push projects forward.
Asset management has always been a challenge. But in today’s landscape—marked by the labor shortage, high equipment and materials costs, and supply chain uncertainty—managing and tracking your assets manually has grown increasingly difficult.
That’s why contractors have turned to automation.
Automation can eliminate repetitive asset tracking tasks provide each departments with the data they need, improving operational efficiency and unlocking better project outcomes.
In this article, we’ll break down 8 ways asset tracking automation helps your field, warehouse, and back-office teams increase productivity to accelerate project delivery and increase profit margins.
