Liebherr Unveils its First Autonomous, Electric T 264 Dump Truck
The unveiling of the 240-metric-ton-payload hauler also included Liebherr’s new electric-drive excavator and plans for an electric...
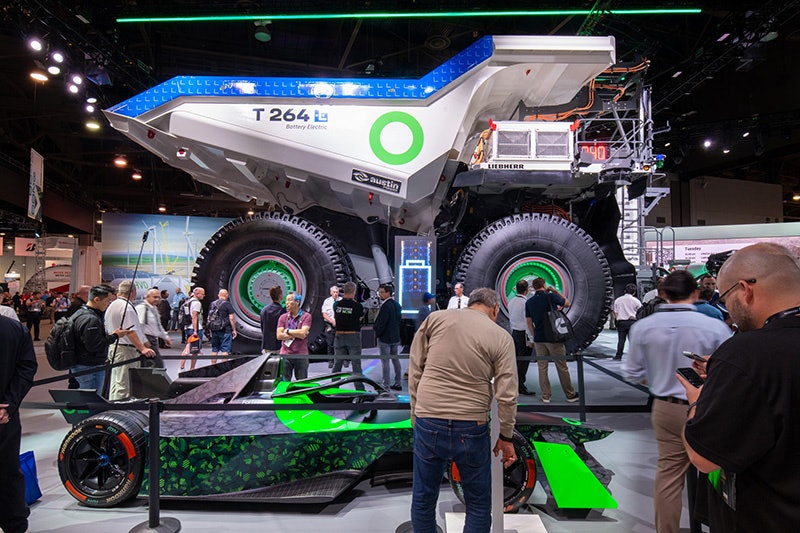
Liebherr has teamed up with Australian mining giant Fortescue to bring battery electric to some of the largest mining machines in the world, as well as autonomy.
At last week’s Minexpo in Las Vegas, the partners revealed Liebherr’s first autonomous, battery-electric T 264 rigid-frame dump truck. The partnership marks Liebherr’s largest equipment deal in its 75-year history.
The unveiling of the 240-metric-ton-payload, electric, autonomous hauler also included Liebherr’s new 400-metric-ton R 9400 E electric-drive excavator and plans to develop an electric version of its 70-metric-ton PR 776 dozer.
The mining truck runs on a 3.2-megawatt-hour battery developed by Fortescue Zero, the iron-ore mining company’s technology arm. The companies said they have also developed a static charging solution for the big hauler that can quick charge its batteries in 12 to 58 minutes.
The truck is equipped with the Autonomy Haulage Solution to coordinate truck recharging at the mine site to prevent trucks from lining up and waiting to be recharged, the companies say.
Autonomous, Electric Hauler
Liebherr
The new fleet of trucks has been arriving at Fortescue’s Western Australia operations since October. The first trucks are diesel-powered models being converted to electric, but most of the fleet will eventually be supplied as battery-electric configurations, the companies say.
Fortescue already has four autonomous Liebherr T 264s being tested, with fully operational autonomous models set for the first quarter of 2025. Testing is expected to be completed in early 2026.
The companies add that the battery system and Autonomous Haulage Solution can be used to retrofit Liebherr diesel trucks. “This means that trucks purchased today are already futureproofed for tomorrow,” the companies say.
The static charger for the truck was developed by Fortescue. It comes in manual or robotic versions with an automatic quick charger of up to 6 megawatts that can charge the current battery-electric T 264 in 30 minutes. No word yet on runtime for the trucks.
The battery system is not all that is designed for reducing carbon-dioxide emissions. The trucks will be equipped with Michelin’s energy-efficient XDR Energy tires. The tires, said to be the first designed for energy efficiency for the mining industry, are made with an energy-saving rubber compound and optimized tread, the companies say.
They claim a 3.6% reduction in fuel consumption in flat conditions compared to Michelin’s XDR 250 C tires on combustion-engine trucks.
R 9400 E Electric-Drive Excavator
In 2023, Liebherr Mining achieved its first repower of a diesel-drive machine to electric drive, the R 9400 E excavator.Liebherr
The mining company got its first of the “repowered” 400-metric-ton excavators in December.
Three R 9400 E excavators are already operational across Fortescue’s sites, the companies say.
The excavators were converted from diesel to electric-drive systems. Liebherr sees the conversion as being able to prevent mine owners from having to get rid of diesel machines, to save money yet still reduce emissions.
“Repowering to an electric excavator can also offer the additional benefits of faster loading cycle times and improved hydraulic pump component life, thanks to the constant shaft speed of the electric motor,” according to Liebherr.
The electric system on the converted excavators can be installed in weeks, Liebherr says. It involves removing the diesel powerpack and fuel tank and replacing them with electric counterparts – “in this case, an electric-drive powerpack and a high-voltage electric cabinet.” A new rotary connection is also installed.
PR776 Electric Dozer
Liebherr's PR 776 dozer is slated for conversion to battery-electric.Liebherr
The new electric dozer is currently being developed. Fortescue is on tap to receive 60 of the 70-metric-ton-capacity “zero emission” models.
All 475 machines of this deal will become part of Fortescue’s iron ore hub in the Pilbara region of Western Australia, the companies say. They will make up about two thirds of the current mining fleet at Fortescue’s operations.
Both companies said they “are committed to having a comprehensive and large-scale zero-emission mining ecosystem operational by 2030.”