7 Warning Signs Your Forklift Parts Need Maintenance or Replacement
Forklifts are essential in many workplaces, ensuring smooth and efficient material handling. However, maintaining these machines is critical to prevent costly downtime or safety risks. Neglecting regular inspections or ignoring early warning signs of wear can escalate minor issues into major problems. Ensuring your forklift operates at peak performance involves understanding when its components need […] The post 7 Warning Signs Your Forklift Parts Need Maintenance or Replacement appeared first on World Construction Today.
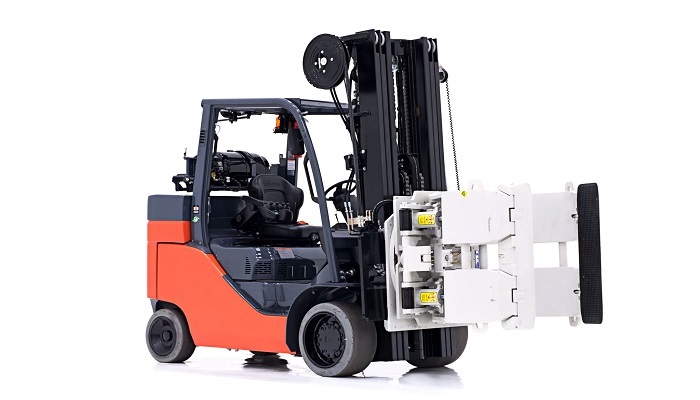
Forklifts are essential in many workplaces, ensuring smooth and efficient material handling. However, maintaining these machines is critical to prevent costly downtime or safety risks. Neglecting regular inspections or ignoring early warning signs of wear can escalate minor issues into major problems. Ensuring your forklift operates at peak performance involves understanding when its components need repair or replacement.
Why Timely Forklift Maintenance Matters
Forklifts are complex machines with numerous interconnected parts, making regular maintenance essential. Addressing issues early ensures small problems don’t get big, spiralling into costly repairs or safety hazards. Here is why you should be proactive about forklift maintenance:
- Safety First: Faulty forklifts pose significant risks to operators and bystanders. Routine maintenance minimises the chances of accidents caused by equipment failures, keeping everyone safe.
- Cost Efficiency: Repairing small issues early prevents them from developing into more expensive problems. Well-maintained forklifts also consume less energy, reducing operational costs.
- Enhanced Productivity: A forklift in excellent condition operates smoothly, ensuring materials are moved efficiently. Malfunctioning equipment slows operations and increases downtime.
- Extended Equipment Lifespan: Regular servicing extends the life of your forklift, ensuring a higher return on your investment and delaying the need for replacement equipment.
- Compliance with Regulations: Proper maintenance helps you adhere to workplace safety standards and regulatory requirements, avoiding penalties.
- Environmental Benefits: Efficient forklifts produce fewer emissions and consume less fuel, aligning with sustainability goals.
Key Indicators Your Forklift Needs Attention
Given the importance of regular maintenance, it’s critical to pay close attention to warning signs that it’s time to service or replace your forklift parts. By addressing these signs promptly, you can maintain workplace safety, productivity, and equipment longevity.
1. Warning Lights on the Information Panel
Modern forklifts have information panels that display warning lights when there’s something. Alerts may indicate issues like low tyre pressure, the need for an oil change, or engine trouble. Suppose there is no such thing on your forklift. In that case, you should make a habit of doing visual inspections before each shift and promptly address any issues.
2. Worn-Out Tyres
Tyres are often the first parts to show wear and tear. Regular inspections are essential to maintaining smooth operations. Watch for these warning signs:
- Excessive Wear: If the tyres have worn down to the brand name, they are nearing the end of their life—usually around 100 hours of use remain. Plan accordingly.
- Chunking: Pieces of rubber breaking off the tyre indicate the need for immediate replacement. Chunking compromises the tyre’s performance and safety.
- Cracks or Tears: These often result from driving over debris or long-term use. Cracked tyres are unsafe and should be replaced immediately.
- Flat Spots or Kinks: These can indicate internal damage or improper weight distribution.
3. Brake Issues
Brakes are critical to the safe use of a forklift. If you notice the following, get a pro to inspect your brakes immediately:
- Spongy Feel: When you step on the brakes, and it feels like you’re stepping on something soft, it means either worn brake pads or low brake fluid levels.
- Squeaking or Grinding Noises: These sounds often point to worn pads or discs that require immediate replacement.
- Slow Response: Your forklift should stop immediately when you step on the brake. Delayed braking action can signal serious underlying issues that need professional attention.
4. Leaking Fluids
Forklifts rely on various fluids for proper functioning, including hydraulic fluid, engine oil, coolant, and transmission fluid. Leaks are a clear indication that something is wrong. Key types of leaks and their implications include:
- Hydraulic Fluid: Essential for lifting and tilting operations, hydraulic fluid leaks are often identified by puddles of amber or reddish fluid near the mast or under the machine. These leaks may result from cracked hoses, corroded fittings, or worn seals. They can compromise lifting capacity and lead to safety hazards.
- Engine Oil: Dark brown or black fluid near the engine area indicates an oil leak, often caused by worn gaskets, cracked oil pans, or damaged oil lines. Left unaddressed, this can cause engine overheating or failure.
- Coolant: Bright green, orange, or pink fluid leaking from the radiator or hoses signals a coolant issue. If ignored, coolant leaks can cause the engine to overheat and cause significant damage.
- Transmission Fluid: Red or brown fluid under the forklift’s centre may suggest issues such as worn seals or a damaged transmission pan.
- Fuel: For gas- or diesel-powered forklifts, fuel leaks present a serious safety hazard, risking fire or explosion. Common signs include the smell of fuel or wet spots near the tank or fuel lines.
- Battery Acid: In electric forklifts, battery acid leaks can corrode components and pose chemical hazards. Watch for white residue around terminals or a sulphuric odour.
Fluid leaks are often accompanied by other performance issues, such as difficulty steering, spongy brakes, or reduced lifting power. Regularly check for stains under parked forklifts and inspect hydraulic hoses and connections for abrasions, cracks, and improper routing. You should replace damaged hoses promptly to prevent further issues.
5. Weird Noises
Forklifts can make a lot of noise, depending on the type. However, some sounds during forklift operation are not normal, often indicating mechanical issues. Examples include:
- Squealing: Often linked to worn mast rollers or chains.
- Grinding: This can indicate transmission or drivetrain problems.
- Rattling: This may suggest loose parts or engine trouble.
- Hissing: A potential sign of hydraulic leaks.
- Clunking: Points to suspension or steering issues.
If you hear strange noises, don’t shrug it off. Trace the source and address the issue immediately.
6. Uneven Fork Tips
You can visually see when something is wrong with the fork tips. Bent or uneven fork tips hinder safe lifting and can damage materials. Use a calliper to check fork wear—if the back teeth pass over the blade, the fork is worn beyond the safe 10% threshold and must be replaced.
7. Excessive Exhaust Fumes
Gas or diesel forklifts producing unusual exhaust fumes may have engine problems. Such fumes can pose health risks to operators and nearby workers. Strong fuel odours often point to clogged filters, which reduce efficiency and cause overheating or engine damage. To maintain performance, regularly inspect and replace oil, air, and fuel filters.
Prioritize Maintenance to Ensure Forklift Safety and Efficiency
Preventative maintenance is key to maximising the useful life of your forklift and avoiding expensive repairs. By promptly addressing issues like worn tyres, fluid leaks, and spongy brakes, you ensure your forklift operates safely and efficiently. Using genuine forklift parts can further enhance reliability and longevity.
Contact a licensed technician immediately if you notice any warning signs or suspect performance issues. Acting swiftly prevents further damage, protects workplace safety, and keeps your operations running smoothly.
The post 7 Warning Signs Your Forklift Parts Need Maintenance or Replacement appeared first on World Construction Today.