How Much Do Steel Buildings Cost? 5 Things To Consider
Steel buildings have become a popular option for a wide range of construction projects due to their durability, flexibility, and cost-effectiveness. Whether used for warehouses, agricultural buildings, workshops, or commercial spaces, the cost of a steel building can vary significantly depending on various factors. Understanding what influences the price will help buyers make informed decisions […] The post How Much Do Steel Buildings Cost? 5 Things To Consider appeared first on World Construction Today.
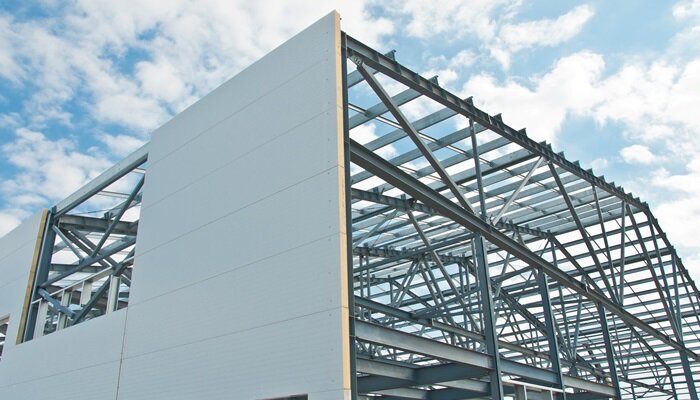
Steel buildings have become a popular option for a wide range of construction projects due to their durability, flexibility, and cost-effectiveness. Whether used for warehouses, agricultural buildings, workshops, or commercial spaces, the cost of a steel building can vary significantly depending on various factors.
Understanding what influences the price will help buyers make informed decisions and potentially save money on their investment.
1. Size and Design of the Building
The size of the steel building is one of the primary factors affecting its cost. Larger structures require more steel, resulting in higher material costs. In addition, larger buildings often necessitate more intricate designs and require professional assembly, which further adds to the expense. On the other hand, smaller steel buildings are generally more affordable and easier to install.
Design complexity also plays a role. While basic rectangular or square buildings are relatively straightforward and inexpensive, more complex designs involving customized dimensions, doors, windows, and other architectural features will drive up costs. Additionally, modifications or expansions in the future could incur further expenses.
When planning a steel building, it’s crucial to assess current and future space requirements. Overestimating or underestimating these needs can significantly impact the overall cost. Many companies such as www.murraysteelbuildings.com and others offer customization options to meet specific design requirements, which can help buyers find the most cost-efficient solution.
2. Material Quality
The quality of the materials used for a steel building can greatly affect its overall price. Steel comes in various grades, and choosing a higher grade will likely result in a more durable structure. However, higher-quality steel is also more expensive. Selecting the right grade of steel is essential, especially if the building will be located in areas prone to extreme weather conditions, as stronger materials will withstand wind, snow, and other elements more effectively.
Buyers should be cautious about opting for cheaper materials that might save costs upfront but could lead to higher maintenance expenses or even structural issues down the line. High-quality, corrosion-resistant steel may come with a higher initial cost, but it often provides better long-term value by reducing maintenance needs and extending the building’s lifespan.
3. Location and Site Preparation
The location where the steel building will be erected plays a significant role in determining its cost. Not only do land prices vary greatly depending on the region, but geographical factors such as soil conditions, weather patterns, and seismic activity can also influence the total price. For example, buildings in regions with heavy snowfalls may require reinforced roofs, which will increase both material and labor costs. Similarly, if the site is in a hurricane-prone area, additional bracing may be needed.
Site preparation costs also need to be considered. This includes leveling the land, installing a foundation, and ensuring proper drainage. Complex sites that require extensive grading or clearing will add to the total project costs. Furthermore, locations far from manufacturing plants or suppliers may incur higher transportation costs, as shipping steel can be costly, especially over long distances.
4. Labor Costs and Installation
While steel buildings are often marketed as easy to assemble, labor costs can still be a significant portion of the total expense. Prefabricated kits, while helpful, may still require skilled professionals to install them correctly and safely. Improper installation can lead to structural issues, so hiring experienced workers is essential. Labor rates vary by region, with metropolitan areas typically commanding higher wages compared to rural regions.
In some cases, businesses or individuals may attempt to erect smaller steel buildings on their own to save on labor costs. While this is possible for those with construction experience, professional installation is recommended for larger or more complex structures. Keep in mind that saving on labor by cutting corners could lead to more expenses down the road due to repairs or maintenance issues.
5. Insulation and Climate Control
Another cost factor to consider is insulation and climate control. Depending on the intended use of the building, proper insulation may be necessary to maintain a comfortable interior environment and protect against condensation. Insulated steel buildings are particularly important for spaces that will be used for living quarters, offices, or storage of temperature-sensitive goods.
Various insulation options exist, including foam panels and fiberglass batts. While these add to the overall cost of the project, they can also lead to energy savings over time by reducing heating and cooling expenses. Buyers should also consider additional climate control features such as HVAC systems, which further increase upfront costs but may be necessary for year-round use in certain climates.
Conclusion
The cost of steel buildings depends on a variety of factors. Understanding these elements will help buyers make informed decisions and potentially reduce expenses without sacrificing quality. With careful planning and attention to detail, a steel building can be an excellent investment for both residential and commercial purposes.
The post How Much Do Steel Buildings Cost? 5 Things To Consider appeared first on World Construction Today.